Introduction to Food X-Ray Inspection
Ensuring food safety is crucial in the food and pharmaceutical industries, as contaminants like bones, glass, metal, and plastics pose serious health risks and can lead to costly recalls. Traditional inspection methods, such as metal detectors, have limitations in detecting non-metallic foreign objects. An X-Ray inspection system provides advanced contaminant detection for packaged and processed products, enhancing quality control and compliance.
The Importance of Contaminant Detection
Foreign objects in food and pharmaceuticals can cause health hazards and legal issues. Unlike metal detectors, food X-Ray inspection equipment detects a wide range of contaminants, including glass, bones, and dense plastics, making it a preferred solution for comprehensive quality control.
Challenges in Detecting Bones, Glass, and Plastics
Low-density materials like bones and plastics blend with food, making detection difficult. Traditional methods struggle with these contaminants, especially in complex food structures or high-speed production. X-Ray inspection machines overcome these challenges using dual-energy imaging and AI-based analysis to enhance accuracy, even in dense or overlapping packaging.
How X-Ray Inspection Improves Safety and Quality
An X-Ray machine for food processing ensures:
High Sensitivity Detection – Identifies bones, glass, ceramics, and plastics.
Compatibility with Various Packaging Types – Works with metalized films and dense food products.
Automated Rejection Mechanisms – Instantly removes contaminated products.
Product Integrity Checks – Detects missing or broken items and ensures weight accuracy.
By integrating an X-Ray inspection system, manufacturers minimize recalls and maintain high safety standards.
How X-Ray Inspection Works
Unlike traditional metal detectors, X-Ray machines for food inspection detect various contaminants based on density and composition. This makes them essential for modern food production lines.
Principles of X-Ray Imaging for Material Differentiation
An X-Ray inspection system emits X-Rays through a product, capturing images where denser materials absorb more radiation. Bones, glass, and metal appear more opaque, making them easier to identify. Dual-energy technology and AI further enhance detection accuracy.
Role of Density, Thickness, and Composition in Detection
Density: High-density materials like glass and metal absorb more X-Rays, making them highly visible.
Thickness: Thicker contaminants block more X-Rays, aiding in precise detection.
Composition: Material differences allow food X-Ray inspection equipment to distinguish foreign objects from food products.
This ensures X-Ray machines for food inspection detect contaminants that metal detectors cannot, improving safety across various food applications.
Detecting Bones in Meat: Challenges and Solutions
Bone detection in meat and seafood processing is critical for food safety. Low-density bones—such as fish, poultry, ribbon, and calcified bones—are challenging to detect using traditional methods. X-Ray machines for food processing provide a more reliable solution.
Challenges in Identifying Low-Density Bones
Thin and Small Structures: Fish and poultry bones are fine and difficult to distinguish.
Fragmentation: Bones break into smaller pieces during processing.
Low Density: Some bones, like young poultry bones, are not fully calcified, making them harder to detect.
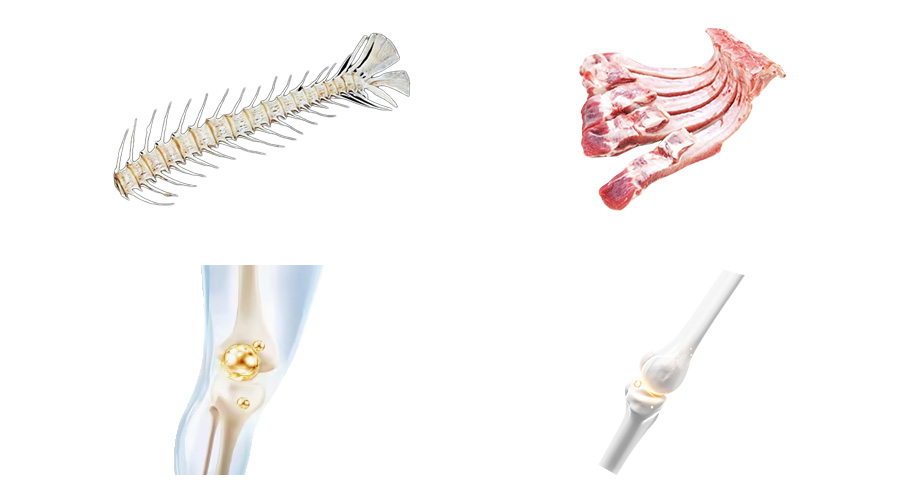
How Dual-Energy X-Ray and AI Enhance Bone Detection
Dual-Energy X-Ray: Captures images at different energy levels, improving bone contrast.
AI-Based Image Processing: Recognizes bone structures, reducing false positives.
Automatic Adaptability: Adjusts detection settings based on product density.
Case Studies in Meat and Seafood Industries
Fish Processing: A seafood company detected fish bones as small as 0.2 mm, reducing complaints.
Poultry Processing: A poultry plant improved bone detection accuracy to over 98%.
Meat Processing: A beef processor used AI-powered food X-Ray inspection equipment to improve detection efficiency.
By using X-Ray inspection machines, manufacturers enhance safety and meet industry standards.
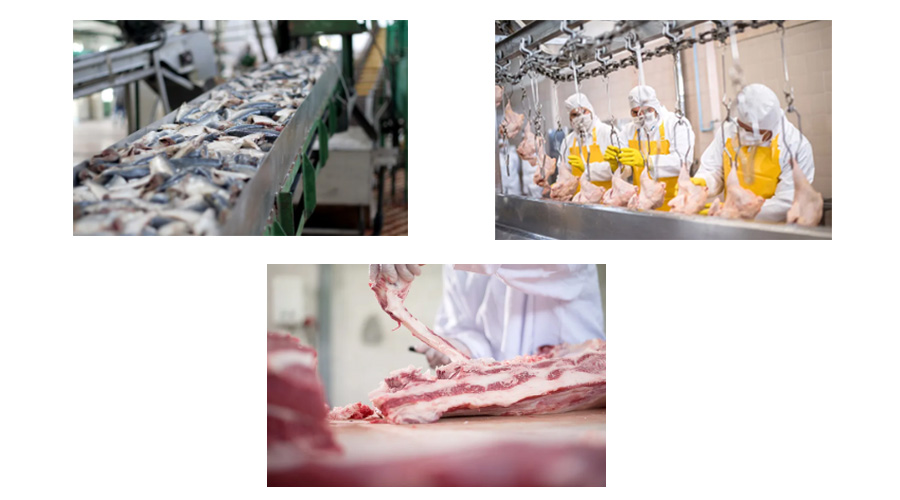
Identifying Glass Contaminants in Food Processing
Glass contamination is a major safety risk, leading to injuries, recalls, and reputational damage. X-Ray machines for food inspection offer superior detection capabilities for glass in various packaging formats.
Why Glass Fragments Are Dangerous
Consumer Safety: Glass fragments cause cuts and choking hazards.
Product Recalls: Contaminated products lead to financial losses.
Regulatory Compliance: Strict standards require effective detection.
How X-Ray Inspection Detects Glass in Different Packaging Types
Bottles and Jars: Identifies glass fragments even in thick packaging.
Pouches and Flexible Packaging: Detects glass inside plastic or foil packs.
Canned Products: Food X-Ray inspection detects glass in metal cans, an advantage over metal detectors.
Ensuring Detection Accuracy for Small and Irregular Glass Pieces
High-Resolution Imaging: Detects glass as small as 1.0 mm.
Multi-Energy Analysis: Differentiates glass from food.
AI Algorithms: Enhances detection accuracy.
With X-Ray machines for food processing, manufacturers prevent hazards and comply with industry regulations.
Plastic Detection: Overcoming Low-Density Challenges
Plastics in food production are challenging to detect due to their low density. X-Ray inspection systems with deep learning algorithms provide effective plastic detection.
Challenges in Detecting Low-Density Plastics
Difficult to Detect: Traditional metal detectors cannot identify plastics.
Health Risks: Ingesting plastic causes choking and digestive issues.
Regulatory Compliance: Stringent safety regulations require improved detection.
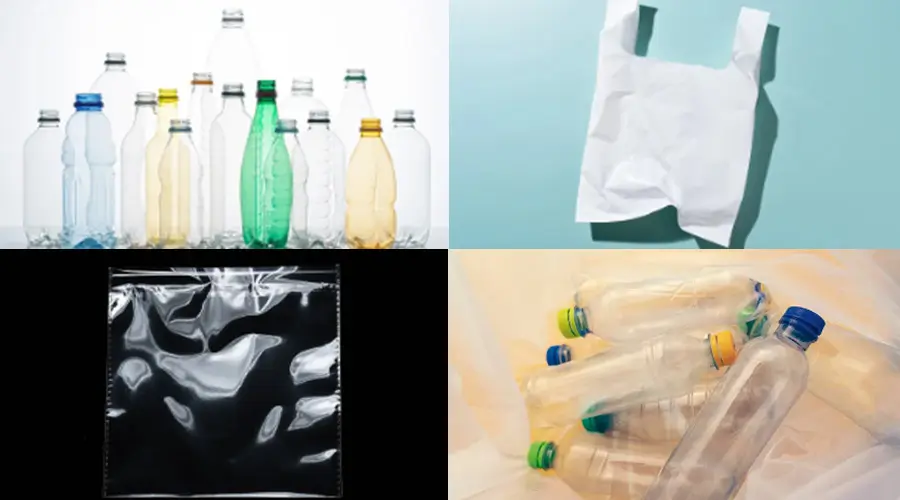
Advanced X-Ray Technology for Plastic Recognition
Dual-Energy X-Ray: Differentiates plastic from food.
High-Resolution Imaging: Identifies even thin plastic fragments.
AI Algorithms: Improves detection accuracy.
Industries Benefiting from Plastic Contamination Detection
Food Processing: Detects plastics in snacks, dairy, and frozen meals.
Meat and Seafood: Prevents plastic residues from processing equipment.
Beverages: Identifies plastic in liquid-filled containers.
Pharmaceuticals: Detects plastic contamination in drug packaging.
By using food X-Ray inspection equipment, manufacturers enhance safety, reduce risks, and maintain compliance with global food safety standards.
The Role of AI and Deep Learning in X-Ray Inspection
Enhancing Detection Accuracy with Intelligent Algorithms
Artificial intelligence (AI) and deep learning have transformed the capabilities of food X-Ray inspection equipment, making detection more precise and efficient. Traditional X-Ray inspection machines rely on predefined algorithms to identify foreign contaminants, but deep learning enables X-Ray machines for food inspection to recognize patterns, detect anomalies, and improve accuracy over time. By analyzing thousands of X-Ray images, AI-powered X-Ray inspection systems can differentiate between normal product variations and potential contaminants, reducing manual intervention and improving reliability.
Reducing False Positives and Improving Efficiency
False positives in food X-Ray inspection can disrupt production and lead to unnecessary product waste. AI-driven X-Ray inspection machines minimize these errors by learning from historical data, refining detection parameters, and reducing misidentifications. This ensures that only contaminated products are rejected while maintaining maximum production efficiency. As a result, manufacturers can optimize their operations while maintaining the highest standards of food safety.
Continuous Learning for Better Adaptability to New Contaminants
The adaptability of AI-powered X-Ray machines for food inspection is a game-changer in food safety. Unlike conventional systems, which require manual reconfiguration for new contaminants, deep learning models continuously evolve by processing real-world inspection data. Whether detecting emerging contaminants like biodegradable plastics or new packaging materials, AI-driven food X-Ray inspection equipment stays ahead of evolving food safety challenges, ensuring comprehensive protection.
Benefits of X-Ray Inspection for Multi-Contaminant Detection
Comprehensive Detection in a Single Pass
Unlike metal detectors, X-Ray inspection systems can identify a wide range of contaminants—including metal, glass, bones, ceramics, rubber, and dense plastics—in one scan. This multi-contaminant detection capability makes X-Ray machines for food inspection essential for industries handling packaged, processed, and bulk food products. Food X-Ray inspection ensures that no harmful substances compromise product quality or consumer safety.
Non-Invasive and High-Speed Inspection for Production Lines
Modern X-Ray inspection machines offer real-time, high-speed scanning without disrupting the production process. These non-invasive systems inspect food products without altering their texture, composition, or packaging, making them ideal for industries with high production volumes. Whether it’s a food X-Ray inspection system for meat, seafood, dairy, or bakery products, these machines help manufacturers maintain efficiency while ensuring compliance with safety standards.
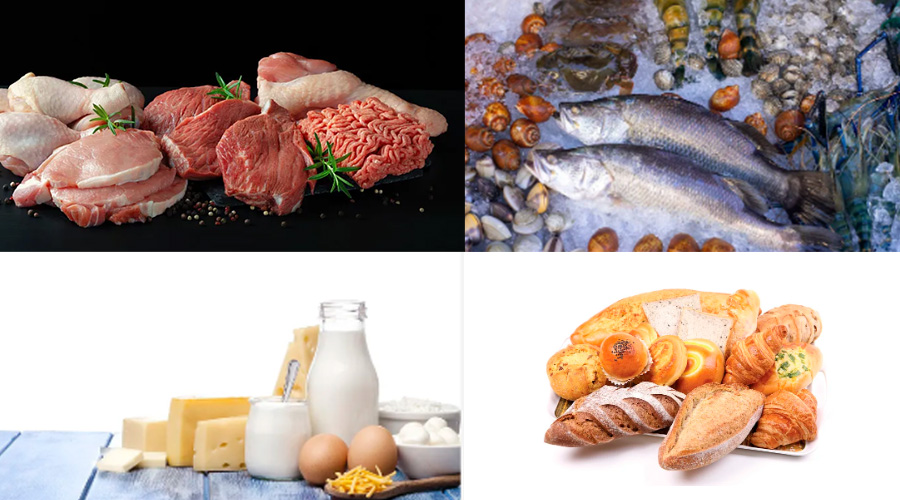
Compliance with Food Safety Regulations (e.g., HACCP, FDA, BRC)
Regulatory compliance is a top priority for food manufacturers. X-Ray inspection machines help businesses meet stringent global food safety standards, including HACCP, FDA, and BRC. By integrating food X-Ray inspection equipment, manufacturers can ensure that their products meet industry regulations, preventing recalls, protecting brand reputation, and maintaining consumer trust.
Future Innovations and Industry Trends
AI-Driven Advancements in X-Ray Detection Technology
Future X-Ray machines for food inspection will feature even more advanced AI models capable of detecting ultra-low-density contaminants, such as soft plastics and organic residues. These innovations will further enhance the accuracy and efficiency of food X-Ray inspection equipment, making them indispensable for quality control in the food and pharmaceutical industries.
Integration with IoT for Real-Time Monitoring and Predictive Maintenance
The next generation of X-Ray inspection systems will integrate with IoT (Internet of Things) technology, enabling real-time monitoring and predictive maintenance. IoT connectivity will allow manufacturers to track machine performance remotely, receive instant alerts for maintenance, and optimize their inspection processes. This ensures minimal downtime and maximum operational efficiency for X-Ray machines for food inspection.
The Future of Fully Automated, Self-Learning Inspection Systems
With continued advancements in AI and automation, food X-Ray inspection equipment will become more autonomous. Self-learning X-Ray inspection machines will adjust sensitivity settings based on production trends, identify new contaminants without human intervention, and optimize inspection performance dynamically. These developments will revolutionize food safety by reducing human error and enhancing product reliability.
Conclusion
The Increasing Necessity of X-Ray Inspection for Food and Pharmaceutical Safety
As food safety regulations become stricter, X-Ray inspection systems are no longer optional—they are essential. Manufacturers must invest in food X-Ray inspection technology to protect consumers, prevent contamination, and comply with international standards.
How Businesses Can Leverage Advanced X-Ray Solutions to Enhance Product Quality
By integrating X-Ray machines for food inspection, businesses can streamline quality control, reduce recall risks, and improve operational efficiency. Whether detecting bones in meat, glass in packaged goods, or plastics in processed foods, food X-Ray inspection equipment provides unparalleled safety assurance.
The Role of Innovation in Shaping the Next Generation of Contaminant Detection
The future of X-Ray inspection machines lies in AI-driven automation, IoT connectivity, and enhanced detection capabilities. As technology evolves, food X-Ray inspection will continue to set new benchmarks for food safety, ensuring that manufacturers can confidently deliver high-quality, contamination-free products to the market.
By adopting X-Ray inspection systems, businesses can stay ahead of food safety challenges, enhance consumer trust, and maintain a competitive edge in the industry.