Introduction: The Need for Advanced Quality Control in Packaged Food
In today’ s competitive market, X-Ray inspection technology has become an essential tool for ensuring packaged food quality. As more manufacturers seek better ways to detect contaminants and defects without damaging products, the X-Ray Inspection system stands out as a proven, non-destructive solution. These advanced machines help businesses protect their brand reputation and meet the growing demands for food safety.
Increasing Consumer Expectations for Safe and High-Quality Food
Consumers today expect not only delicious and convenient food but also the highest safety and quality standards. To meet these expectations, many manufacturers are implementing X-Ray inspection machines that offer superior detection capabilities compared to traditional inspection methods. With the ability to identify foreign objects like metal, glass, or stone, X-Ray Inspection systems play a critical role in building consumer trust and loyalty.
The Challenges of Maintaining Consistency and Quality in Packaged Food
Maintaining consistent quality across high-speed production lines presents many challenges, from detecting tiny contaminants to ensuring proper packaging integrity. Traditional inspection methods often fall short, especially when products are complex or densely packed. That’s why manufacturers are increasingly relying on X-Ray inspection technologies, as an X-Ray inspection machine can detect even the smallest irregularities without interrupting production flow.
How X-Ray Systems are Transforming the Food Quality Control Process
X-Ray Inspection systems are revolutionizing quality control in the packaged food industry by offering real-time, automated detection of a wide range of contaminants. These systems provide unmatched accuracy, minimize false rejects, and allow for higher production efficiency. By integrating X-Ray inspection into their production lines, manufacturers not only improve food safety but also significantly enhance operational performance and regulatory compliance.
Traditional Quality Control Methods vs. X-Ray Systems
In the packaged food industry, traditional quality control methods have long been used to ensure product safety and consistency. However, with increasing consumer expectations and stricter regulations, many manufacturers are turning to X-Ray inspection technologies to achieve more accurate and efficient results. The X-Ray Inspection system has proven to outperform conventional methods in both detection sensitivity and operational speed.
Manual Inspections and Their Limitations
Manual inspection methods rely heavily on human vision and judgment, which can lead to inconsistencies and missed contaminants, especially during high-speed production. Fatigue, distraction, and limited visibility often result in errors that can compromise food safety. In contrast, an X-Ray inspection machine offers continuous, objective, and precise screening, identifying foreign materials invisible to the human eye and greatly reducing the risk of unsafe products reaching consumers.
The Rise of Automated Inspection Solutions in the Food Industry
To overcome the limitations of manual inspections, the food industry has increasingly adopted automated solutions like X-Ray Inspection systems. These advanced machines provide real-time analysis, automatically detecting and rejecting contaminated products without slowing down production. As automation becomes the standard, X-Ray inspection plays a key role in helping manufacturers maintain high safety and quality standards efficiently.
Key Advantages of X-Ray Technology Over Conventional Methods
Compared to traditional inspection techniques such as metal detection or visual checks, X-Ray inspection offers several significant advantages. An X-Ray inspection machine can detect a wide range of contaminants—including metal, glass, stone, bone, and dense plastics—that other methods might miss. Additionally, X-Ray Inspection systems can assess product shape, mass, and integrity, ensuring both food safety and consistent quality. This comprehensive capability makes X-Ray technology a critical asset for modern food manufacturers.
How X-Ray Systems Improve Food Safety and Quality
Modern X-Ray Inspection systems are revolutionizing how manufacturers ensure food safety and quality. By providing unparalleled detection capabilities and non-destructive analysis, these technologies help identify foreign materials, packaging issues, and inconsistencies in products that traditional methods often miss. The use of X-Ray inspection has become essential in maintaining the highest standards in packaged food production.
Detection of Foreign Contaminants (Metal, Glass, Plastic, Stones)
One of the primary strengths of an X-Ray inspection machine is its ability to detect a wide variety of contaminants, including metal fragments, broken glass, hard plastics, and even stones. Unlike traditional metal detectors, which are limited to metallic objects, X-Ray inspection can identify non-metallic foreign bodies, providing broader and more reliable protection against contamination risks.
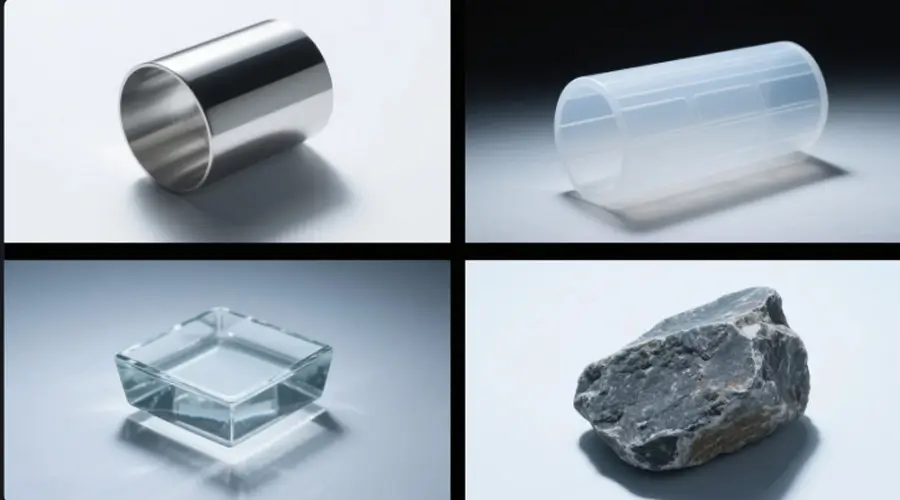
Identifying Defects in Packaging, Such as Seal Integrity Issues
Beyond detecting internal contaminants, an advanced X-Ray Inspection system can also reveal packaging defects such as improper seals, trapped air pockets, or leaks. Ensuring seal integrity is critical for maintaining product freshness and preventing spoilage. With X-Ray inspection, manufacturers can address these issues before the product reaches consumers, enhancing overall product quality and safety.
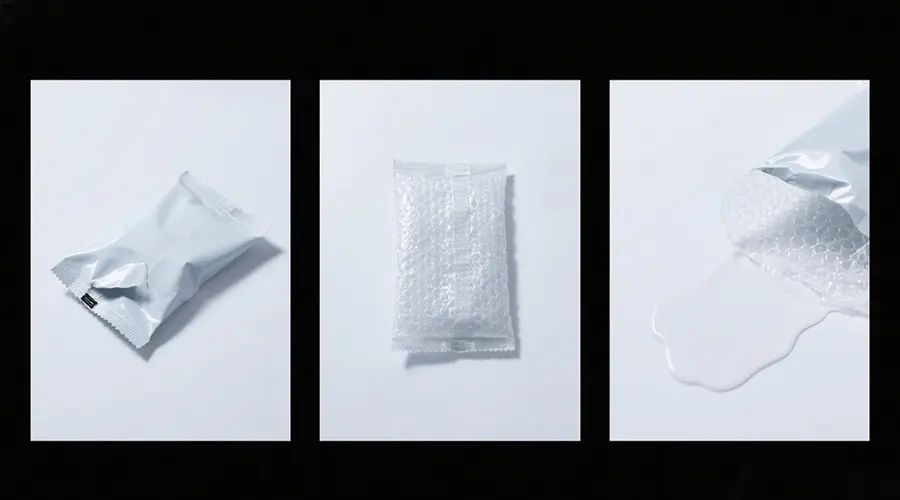
Ensuring Consistency in Product Weight, Shape, and Fill Levels
Consistency in product presentation is a key factor in customer satisfaction. X-Ray inspection machines can accurately measure the weight, shape, and fill levels of packaged goods without opening or damaging them. This ensures that every product meets quality standards, helping brands maintain a consistent image and reduce complaints related to underfilled or misshapen products.
Monitoring for Undetected Foreign Objects Without Damaging Products
Traditional detection methods often involve invasive techniques that risk damaging the product. However, X-Ray inspection offers a non-destructive solution, allowing for thorough internal examination without compromising the packaging or the food itself. This capability ensures that products remain intact while maintaining the highest safety and quality standards.
Specific Applications of X-Ray Systems in Packaged Food Industry
X-Ray inspection systems are widely used across various sectors of the packaged food industry, offering precise, non-destructive detection capabilities. From snacks to frozen meals, the use of X-Ray inspection machines ensures product safety, consistency, and quality while meeting regulatory demands and consumer expectations.
X-Ray Inspection in Snacks and Confectionery Products
Snacks and confectionery items, often produced in high volumes, are susceptible to foreign material contamination during manufacturing. X-Ray inspection systems can detect contaminants such as small metal fragments, glass shards, or dense plastic pieces that may accidentally enter products like chocolates, candies, or chips. Using X-Ray inspection helps maintain the safety and reputation of brands by ensuring only defect-free products reach consumers.
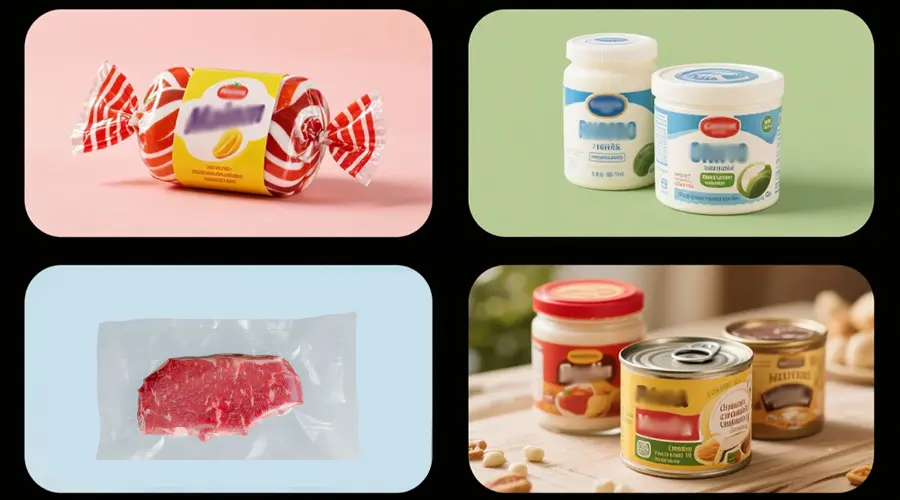
Using X-Ray Systems for Meat and Poultry Packaging
In meat and poultry processing, ensuring the absence of bone fragments, metal shavings, or other foreign objects is crucial. X-Ray inspection machines are highly effective at scanning packaged meat cuts, sausages, and poultry products. The high-resolution imaging capabilities of an X-Ray inspection system allow for the early identification and automatic rejection of compromised packages, significantly reducing the risk of recalls and protecting public health.
Detecting Contaminants in Ready-to-Eat Meals and Dairy Products
Ready-to-eat meals and dairy products are often multi-component foods that can hide contaminants deep inside. X-Ray inspection offers an advanced solution by detecting foreign bodies even through complex or overlapping textures. Whether it’s a convenience meal or a yogurt cup, an X-Ray inspection machine ensures that safety checks are performed without damaging the product, providing both manufacturers and consumers with greater confidence.
Importance in Handling Frozen and Canned Foods
Frozen and canned foods are sealed environments where contaminants are especially hard to detect using conventional methods. X-Ray inspection systems excel in inspecting these products by penetrating through packaging materials and identifying hidden threats like stones, bone fragments, or metallic debris. Employing X-Ray inspection ensures that even products locked in hard-to-see containers are thoroughly examined, enhancing overall food safety.
Benefits of Implementing X-Ray Systems in Food Packaging Lines
Introducing X-Ray inspection systems into food packaging lines brings significant improvements in detection capabilities, production efficiency, regulatory compliance, and cost control. Here’s how X-Ray inspection machines are transforming modern food manufacturing:
Increased Detection Sensitivity and Accuracy
Compared to traditional inspection methods, X-Ray inspection systems offer superior sensitivity and precision. They can detect a wide range of contaminants, including tiny metal fragments, glass pieces, stones, and dense plastics, that might be missed by metal detectors or visual checks. This enhanced accuracy helps manufacturers maintain the highest safety and quality standards, ensuring that only defect-free products reach consumers.
Real-Time Analysis and Automated Product Rejection
X-Ray inspection machines provide real-time imaging and analysis, allowing for immediate identification of contaminated or defective products. Integrated automatic rejection systems promptly remove compromised items from the production line without halting operations. This capability not only safeguards product integrity but also streamlines workflow and minimizes manual intervention.
Enhanced Production Efficiency and Reduced Downtime
By incorporating X-Ray inspection into packaging lines, manufacturers experience fewer disruptions caused by manual inspections or quality issues. The automated and continuous monitoring provided by X-Ray inspection systems helps detect problems early, preventing larger issues that could cause line stoppages. This leads to higher overall efficiency, improved throughput, and lower maintenance downtime.
Compliance with Food Safety Standards (HACCP, FDA, etc.)
Global food safety regulations, including HACCP and FDA standards, require rigorous contaminant detection processes. X-Ray inspection machines are designed to meet or exceed these regulatory requirements. Implementing an X-Ray inspection system not only simplifies compliance audits but also strengthens a brand’s reputation for delivering safe, high-quality products.
Minimizing Product Waste and Reducing Costly Recalls
Effective X-Ray inspection helps manufacturers minimize product waste by accurately identifying only the contaminated or defective items rather than discarding entire batches. This targeted approach reduces material loss and environmental impact. Moreover, early detection of contaminants significantly lowers the risk of costly product recalls, legal issues, and damage to brand reputation.
The Future of Packaged Food Quality Control with X-Ray Technology
As the food industry continues to prioritize safety, consistency, and efficiency, X-Ray inspection systems are becoming more integral to quality control. The future of packaged food quality control lies in the continuous evolution of X-Ray inspection machines, leveraging new technologies and methodologies to address emerging challenges and meet evolving consumer demands.
Advancements in X-Ray Technology and Their Impact on Food Safety
In recent years, X-Ray technology has made tremendous advancements, particularly in the areas of sensitivity, speed, and the ability to detect a wider variety of contaminants. Modern X-Ray inspection systems now feature higher-resolution imaging, allowing for more precise identification of foreign bodies in food products, such as smaller metal fragments, glass, or even dense plastic. These advancements have significantly improved food safety standards, enabling manufacturers to detect and remove contaminants that might have gone unnoticed with older systems. As a result, consumers can enjoy safer products, and manufacturers benefit from lower rates of recalls and customer complaints.
The Role of AI and Machine Learning in Enhancing X-Ray Detection
Artificial intelligence (AI) and machine learning (ML) are revolutionizing X-Ray inspection technology, making it smarter and more capable of handling complex detection tasks. AI algorithms can analyze the X-ray images produced by X-Ray inspection machines with incredible speed and accuracy, allowing for the identification of even the smallest defects or foreign objects in real-time. Machine learning models can continually improve the system’s performance over time, adapting to new types of contaminants or subtle variations in product appearance. This results in more efficient inspections, greater consistency in product quality, and fewer false positives, which in turn lowers the cost of operation.
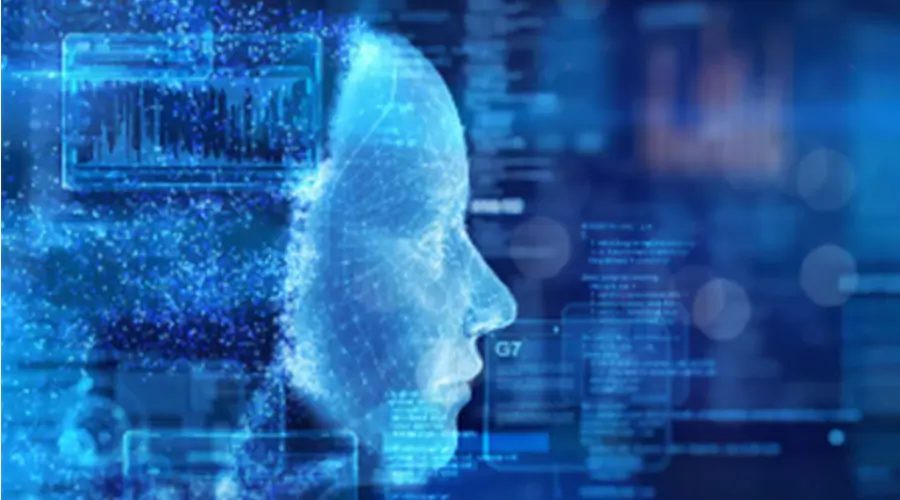
The Growing Adoption of X-Ray Systems Across the Global Food Industry
As food safety regulations tighten and consumer awareness grows, the adoption of X-Ray inspection systems is expanding across the global food industry. From large multinational food producers to smaller, specialty manufacturers, more companies are recognizing the value of X-Ray inspection machines in their quality control processes. The growing demand for safer, higher-quality food products is driving investments in X-Ray inspection technology, with systems becoming more affordable and accessible to companies of all sizes. This trend is expected to continue as food manufacturers seek to meet increasingly stringent safety standards and consumer expectations.
Conclusion: The Critical Role of X-Ray Systems in Revolutionizing Food Quality Control
The food industry is facing increasing pressure to meet higher safety standards, ensure product quality, and satisfy the growing consumer demand for transparency and reliability. X-Ray inspection systems are playing a pivotal role in this transformation, offering a advanced solution to these challenges and revolutionizing how manufacturers approach quality control in packaged food.
The Continuous Evolution of Food Safety Standards
As global food safety standards continue to evolve, manufacturers must stay ahead of regulations and consumer expectations. Regulatory bodies, such as the FDA and HACCP, have set higher benchmarks for contamination detection, product consistency, and traceability. The X-Ray inspection system has become indispensable in this context, allowing food manufacturers to meet these stringent requirements with greater accuracy and efficiency. With the continuous evolution of food safety standards, X-Ray inspection machines provide a flexible, adaptable tool that can keep pace with new challenges in food production, ensuring that food safety and quality are never compromised.
Why Every Food Manufacturer Should Consider X-Ray Technology for Long-Term Success
Investing in X-Ray technology is no longer optional for food manufacturers who want to maintain a competitive edge in today’s market. Not only do these systems provide accurate detection of foreign contaminants, but they also streamline production processes, enhance product consistency, and reduce costly recalls. By integrating X-Ray inspection into their production lines, manufacturers can build stronger relationships with consumers by assuring them of the highest standards of safety and quality. Moreover, X-Ray inspection machines help reduce waste, improve operational efficiency, and ensure compliance with evolving food safety standards, paving the way for long-term success and sustainability in the food industry.
As food safety continues to be a top priority, X-Ray systems will remain a crucial investment for any food manufacturer aiming to maintain product integrity and consumer trust while keeping up with the industry’s evolving demands.